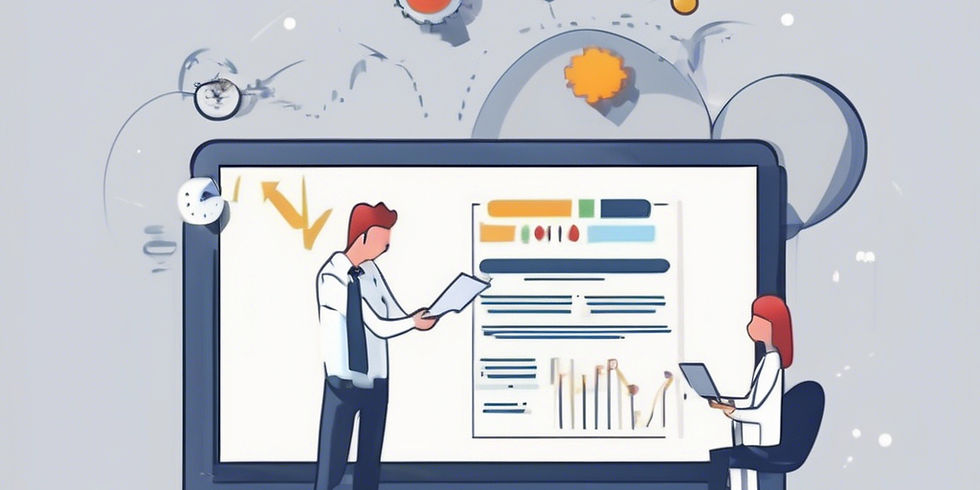
Introduction
Quality management is a fundamental pillar of organizational success, ensuring efficiency, consistency, and customer satisfaction. ISO 9001:2015, the global standard for quality management systems (QMS), provides a structured approach to achieving operational excellence. Internal audits play a crucial role in ensuring compliance with ISO 9001 by assessing processes, identifying inefficiencies, and driving continuous improvement.
1. Understanding ISO 9001:2015
ISO 9001 is an internationally recognized standard that establishes requirements for a robust quality management system. It helps organizations:
✔ Enhance product and service quality.
✔ Improve customer satisfaction.
✔ Optimize operational efficiency.
✔ Ensure regulatory compliance.
Key Clauses of ISO 9001:2015
The ISO 9001 standard is structured around 10 clauses, with internal audits primarily focusing on:
Scope – Defines the applicability of the QMS.
Normative References – Standards referenced within ISO 9001.
Terms and Definitions – Common terminology used in quality management.
Context of the Organization – Understanding internal & external factors influencing quality.
Leadership – Senior management’s role in quality commitment.
Planning – Risk-based thinking and setting quality objectives.
Support – Resource allocation, competence, communication.
Operation – Execution of QMS processes and controls.
Performance Evaluation – Monitoring and measuring QMS effectiveness.
Improvement – Corrective actions and continuous improvement initiatives.
2. Role of Internal Audits in ISO 9001 Compliance
Internal audits serve as a self-regulation tool to ensure that the quality management system is functioning effectively and aligned with ISO 9001 standards.
A. Purpose of Internal Audits
Verify compliance with ISO 9001 requirements.
Identify gaps, non-conformities, and improvement areas.
Ensure the effectiveness of quality processes.
Enhance risk management and process control.
Prepare for external certification audits.
B. Types of Internal Audits in ISO 9001
🔹 System Audit – Evaluates overall QMS effectiveness.
🔹 Process Audit – Assesses the efficiency of specific processes.
🔹 Product Audit – Examines product/service conformity to quality standards.
🔹 Supplier Audit – Reviews supplier performance and adherence to quality guidelines.
3. Internal Audit Process for ISO 9001
To strengthen quality management, organizations must conduct structured internal audits. The process includes:
Step 1: Audit Planning
✔ Define audit objectives, scope, and criteria.
✔ Establish an audit schedule covering all critical areas.
✔ Assign trained internal auditors.
Step 2: Conducting the Audit
✔ Gather evidence through document reviews, interviews, and process observations.
✔ Compare findings against ISO 9001 requirements.
✔ Identify non-conformities and areas for improvement.
Step 3: Reporting & Documentation
✔ Document findings in an internal audit report.
✔ Classify issues as major/minor non-conformities.
✔ Recommend corrective actions and preventive measures.
Step 4: Corrective Action & Follow-Up
✔ Implement corrective measures to address non-conformities.
✔ Conduct follow-up audits to verify effectiveness.
✔ Maintain records for continuous improvement tracking.
4. Challenges in Implementing ISO 9001 Internal Audits
While internal audits are essential, organizations may encounter challenges such as:
❌ Lack of auditor competence – Need for trained professionals with ISO 9001 expertise.
❌ Resistance to change – Employees may resist audit recommendations.
❌ Insufficient resources – Limited time, budget, or tools for audits.
❌ Poor documentation – Failure to maintain proper records for compliance.
Solution Strategies:
✔ Train internal auditors in ISO 9001 audit methodologies.
✔ Foster a culture of quality where audits are viewed as opportunities for improvement.
✔ Implement automated QMS tools for better tracking and documentation.
5. Benefits of ISO 9001 Internal Audits
Internal audits provide multiple advantages in strengthening quality management systems:
✔ Improved Process Efficiency – Identify inefficiencies and optimize operations.
✔ Enhanced Customer Satisfaction – Ensures product/service quality consistency.
✔ Stronger Compliance – Helps maintain adherence to ISO 9001 and regulatory requirements.
✔ Continuous Improvement – Drives a culture of ongoing enhancement and innovation.
✔ Better Decision-Making – Provides data-driven insights for management.
6. The Future of Internal Audits in Quality Management
With advancements in technology and automation, the future of internal audits is evolving:
✔ AI & Data Analytics – Predictive quality analytics for real-time monitoring.
✔ Automated Auditing – Digital QMS tools for seamless compliance tracking.
✔ ESG Integration – Aligning ISO 9001 with sustainability and environmental standards.
✔ Remote Audits – Virtual assessments using cloud-based QMS platforms.
Conclusion
Internal audits are the backbone of a robust ISO 9001 quality management system, ensuring compliance, efficiency, and continuous improvement. By following a structured audit approach, organizations can enhance process effectiveness, mitigate risks, and maintain competitive excellence.
To stay ahead in quality management, invest in trained auditors, automated QMS tools, and a strong audit culture. Strengthen your internal audits today and build a future-ready quality management system!
Comments